Touratech: Produzione
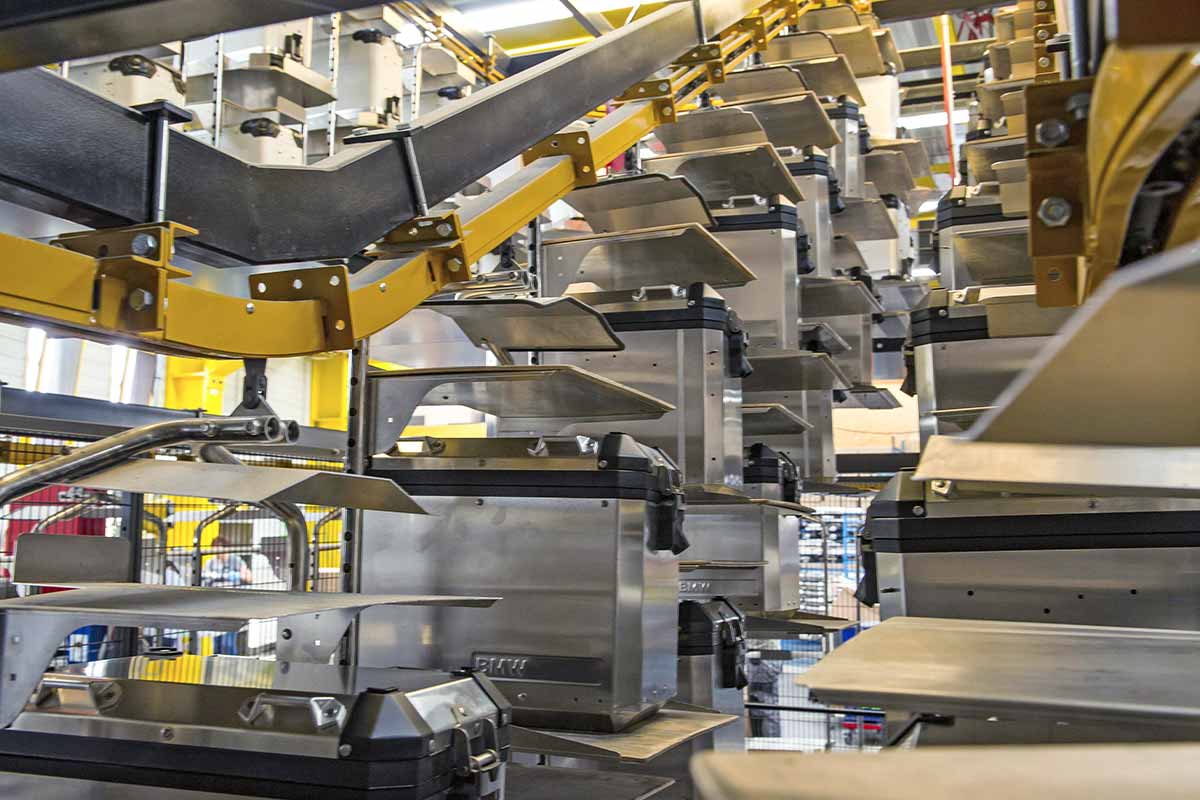
Touratech punta costantemente sul “Made in Germany”. Brevi tempi di consegna, trasparenza delle catene di fornitura e dei processi di produzione, nonché una disponibilità di manodopera qualificata di prim'ordine nella regione sono solo alcuni dei motivi alla base di questa decisione aziendale sostenibile.
Touratech investe continuamente nella sede di Niedereschach per garantire processi di produzione all'avanguardia e una logistica fluida. Le macchine utensili e i centri di lavorazione utilizzati da Touratech, infatti, sono tra i migliori e più veloci sul mercato. Nella produzione di Touratech sono utilizzati in totale 11 robot di saldatura (dall'11/2023) per saldare strutture in alluminio o acciaio inossidabile. Un magazzino di lamiere completamente automatizzato lavora senza interruzioni con tre macchine automatiche combinate laser e punzonatrici laser. La pianificazione e il controllo della produzione (PPS) all'avanguardia garantiscono poi un utilizzo ottimale delle macchine e contribuiscono quindi a una produzione economicamente vantaggiosa. Un edificio logistico dotato della più recente tecnologia a scaffalature verticali consente la consegna rapida di tutti i prodotti Touratech a distributori e clienti in tutto il mondo. Dalla fine del 2023, nello stabilimento vengono prodotte anche le valigie in plastica per il sistema di bagagli Vario di BMW Motorrad.
Touratech è il partner per lo sviluppo e la produzione del sistema di bagagli Vario di BMW Motorrad
A parte il materiale, il sistema di bagagli Vario di BMW Motorrad ha poco in comune con le valigie in plastica convenzionali. Le valigie sono dotate di illuminazione interna, radiocomando per il meccanismo di chiusura tramite la chiave del veicolo e, novità assoluta a livello mondiale, regolazione continua del volume. In una gara d'appalto impegnativa, Touratech è stata scelta non solo come partner per la produzione in serie del sistema, ma anche per il suo sviluppo. Gli sviluppatori di Touratech hanno stabilito nuovi standard con numerose soluzioni innovative, come la regolazione del volume azionata da una cinghia dentata.
Touratech ha implementato un processo di produzione altamente standardizzato e trasparente per produrre in serie la sofisticata tecnologia a un livello costantemente elevato. Invece di una classica linea di assemblaggio, le custodie vengono completamente assemblate passo dopo passo da uno o due dipendenti in un “flusso a pezzo unico” dopo il pre-assemblaggio. Per garantire la massima affidabilità del processo, Touratech ha implementato un avanzato sistema di guida dei lavoratori in cui sono memorizzate tutte le fasi del processo di assemblaggio. Inoltre, ogni custodia è dotata di una scheda RFID che la accompagna dall'inizio alla fine della produzione e la rende chiaramente identificabile.
Per facilitare la formazione, è possibile richiamare grafici o video esplicativi per ogni fase di lavoro su un piccolo schermo direttamente dalla postazione di lavoro. Per le fasi di lavoro importanti, come l'avvitamento, il cacciavite viene regolato automaticamente in termini di coppia e numero di giri.
Una volta che la valigia ha superato l'assemblaggio finale, il pacchetto di dati raccolti durante il processo viene trasferito al controllo di fine linea e valutato. Se tutti i valori rientrano nell'intervallo target, un robot progettato dalla consociata di Touratech, Moldes Epila, testa tutte le funzioni meccaniche ed elettriche della valigia Vario con la massima precisione di ripetibilità.
Touratech è il partner di sviluppo e produzione per la borsa Adventure di BMW Motorrad
IOltre a produrre per l'enorme portafoglio prodotti con il proprio marchio, Touratech è un importante fornitore dell'industria motociclistica da tre decenni. Marchi premium come BMW, Ducati e KTM si affidano alla proverbiale qualità Touratech e fanno produrre i prodotti per il loro programma di accessori originali presso lo stabilimento di Niedereschach. E non è tutto: oltre alla produzione, Touratech si occupa anche dello sviluppo completo per conto dei propri clienti. Un esempio importante: il sistema di valigie in alluminio per la BMW R 1300 GS Adventure per la quale Touratech ha sviluppato la soluzione più avanzata in questo segmento, dal meccanismo di chiusura unico alla complessa struttura del robusto corpo all’elettrificazione.
Circa 150 colleghi producono fino a 1.650 valigie in alluminio alla settimana per BMW Motorrad su una linea di assemblaggio dedicata, suddivisa in tre turni. I dipendenti, che hanno seguito una formazione intensiva, lavorano a stretto contatto con una tecnologia robotica all'avanguardia in un flusso di lavoro computerizzato che garantisce un livello di qualità costantemente elevato.
L'ispezione finale, a cui ogni singola valigia viene sottoposta prima di lasciare la fabbrica, comprende oltre 100 criteri. Il modernissimo sistema logistico Touratech garantisce infatti che le valigie arrivino alla BMW imballate con cura e in tempo.
Produzione delle valigie
Oltre al know-how acquisito in oltre 30 anni di costruzione di valigie in alluminio, i macchinari all'avanguardia sono il secondo pilastro importante per la leggendaria qualità delle valigie in alluminio ZEGA. La lavorazione della materia prima è completamente automatizzata per evitare danni alle superfici. I fogli di alluminio vengono tagliati esclusivamente al laser. Questo vale sia per il materiale del guscio, che viene tagliato utilizzando laser piani all'avanguardia per garantire geometrie esterne e schemi di foratura precisi, sia per le basi e i coperchi imbutiti, che vengono tagliati con precisione utilizzando un laser 3D dopo la formatura.
Proprio come le fasi di lavorazione per la lavorazione dei pezzi formati sono raggruppate in una cella di lavorazione interconnessa e completamente automatizzata, anche le fasi più importanti per la produzione del guscio della valigia avvengono in un centro di lavorazione automatizzato.
Nonostante l'elevato grado di automazione, nella produzione delle valigie sono necessari numerosi dipendenti qualificati. Ciò vale per il funzionamento e il monitoraggio dei centri di lavorazione, nonché per l'assemblaggio dei singoli componenti.
Il montaggio del sofisticato design richiede, infatti, la massima precisione. Per garantire che nulla vada storto nonostante i dipendenti siano altamente qualificati, la produzione Touratech ha un sistema di controllo qualità a maglie strette.
32 dipendenti lavorano su due turni nella produzione vera e propria delle valigie, e circa 130 colleghi se si include la produzione dei supporti e delle parti aggiuntive.
Non sono solo i clienti Touratech a beneficiare dell'esperienza unica dell'azienda nello sviluppo e nella produzione di valigie in alluminio di alta qualità per motociclette. Come dicevamo, infatti, sono numerosi produttori di alta gamma come BMW, Ducati e KTM ad affidarsi a Touratech per la produzione di valigie per la propria gamma di accessori originali. Ogni anno lasciano la fabbrica di Niedereschach circa 100.000 valigie.
Produzione di selle
Dalla base della sella all'anima in schiuma specifica per ogni modello, fino all'applicazione del rivestimento, le selle Touratech sono prodotte con maestria artigianale e tecnologia moderna.
La massima precisione è richiesta già durante lo sviluppo della base della sella, dove i modellisti creano a mano un cosiddetto campione master, sulla base del quale viene costruito lo stampo per la produzione in serie. Touratech utilizza il collaudato processo di stampaggio a iniezione di resina (RIM) per la base della sella. In questo processo, due componenti di una resina sintetica vengono miscelati e iniettati in uno stampo, dove si induriscono rapidamente.
La qualità dell'anima in schiuma è essenziale per il comfort di una sella da moto: per questo motivo gli esperti hanno investito innumerevoli ore nello sviluppo delle schiume. Dal rapporto di miscelazione esatto dei due componenti, alla dimensione dei pori e al volume utilizzato: tutti questi parametri vengono variati innumerevoli volte fino a trovare la composizione perfetta della schiuma. E non esiste una schiuma unica per le selle Touratech. Per ogni modello viene sviluppata infatti una formula individuale.
La forma esatta dell'anima del sedile, che consente una posizione di seduta ergonomicamente corretta e confortevole, viene determinata per ogni modello di moto in un processo complesso.
L'applicazione del rivestimento è la fase finale della produzione del sedile. Esperienza e destrezza sono necessarie per applicare i tessuti all'anima nel miglior modo possibile, in modo che siano tesi e senza pieghe.
Ogni anno vengono prodotti diverse migliaia di selle Touratech. A causa dell'elevata percentuale di lavoro manuale, sono impiegati sette dipendenti appositamente qualificati, dallo sviluppo e produzione della scocca e dell'anima in schiuma alla selleria.
Robot di saldatura
Con una nuova generazione di robot di saldatura, Touratech ha ancora una volta migliorato significativamente la qualità della produzione e ha anche fatto un ulteriore passo avanti nel campo dell'affidabilità dei processi, che è particolarmente importante per gli ordini dei clienti OEM.
Le nuove celle di saldatura sono state sviluppate come progetto congiunto tra Touratech e la sua azienda partner HAPPICH Production Technologies, che, come Touratech, fa parte del Gruppo Happich. Dopo la pianificazione congiunta del progetto e lo sviluppo dei requisiti, MEI ha implementato la tecnologia robotica, mentre i supporti del tavolo di saldatura con i sistemi di bloccaggio ulteriormente migliorati sono di nuovo sviluppi propri di Touratech.
Nella produzione di Touratech sono ora in uso 11 robot di saldatura. Almeno tre sistemi sono sempre utilizzati per la saldatura dell'alluminio, mentre gli altri sono utilizzati per la saldatura di costruzioni in acciaio inossidabile. Idealmente, i sistemi funzionano in un'operazione a due turni senza tempi di inattività.
Per garantire che i robot siano utilizzati nel modo più efficiente possibile, Touratech utilizza uno speciale sistema informatico che coordina con precisione le capacità delle macchine, le risorse del personale e la programmazione della produzione. La programmazione dei robot di saldatura richiede un alto livello di qualificazione. Oltre a una base di esperienza nella programmazione, è necessaria una solida conoscenza della tecnologia di saldatura, per cui in futuro sarà necessario un gran numero di specialisti ben addestrati. L'uso della tecnologia robotica all'avanguardia si inserisce quindi perfettamente nella filosofia di Touratech di produrre prodotti di alta qualità in modo economico presso la sede centrale di Niedereschach, grazie all'interazione tra alta tecnologia e dipendenti altamente qualificati.
Idroformatura
L'idroformatura offre a sviluppatori e progettisti interessanti possibilità per la progettazione dei prodotti. Quando si formano lamiere di alluminio o acciaio inossidabile, ad esempio, il processo consente raggi piccoli quasi arbitrariamente e la precisione di ripetizione del processo è anche molto elevata. In particolare nel settore delle protezioni piatte, come le protezioni per cilindri o motori, l'idroformatura consente forme complesse che garantiscono un aumento significativo della protezione.
Tuttavia, per poter utilizzare il processo per la produzione di accessori per motociclette, gli sviluppatori di Touratech hanno dovuto svolgere un lavoro pionieristico in molti settori. A partire dalla preparazione del lavoro, perché tagliare e preparare la lamiera inserita nella macchina, il cosiddetto grezzo, è tutt'altro che banale. Solo se il grezzo è perfettamente dimensionato, il materiale può fuoriuscire dall'area della flangia nella misura esatta richiesta durante il processo di formatura.
E poi ci sono le enormi pressioni che devono essere controllate nel dispositivo. Va considerato, infatti, che per formare un pezzo grezzo di acciaio inossidabile spesso quattro millimetri sono necessari circa 2.000 bar e oltre.
Anche la costruzione di utensili, che richiede un vasto know-how, non dovrebbe essere trascurata nell'idroformatura. Tuttavia, a differenza della classica imbutitura, è necessaria solo metà dell'utensile, il che è uno dei principali vantaggi del processo. In Crew68 GmbH, Touratech ha al suo fianco un partner di lunga data che ha sviluppato e implementato questo processo internamente nei primi anni.
Dal 2023, Happich CZ s.r.o. ha rilevato la produzione di prodotti idroformati per Touratech GmbH al fine di continuare a realizzare prodotti perfetti per i motociclisti avventurosi in stretta collaborazione con le capacità di taglio laser di componenti in alluminio e acciaio inossidabile di Touratech nella Foresta Nera.